Understanding the Process Behind Professional Packaging Machine Repair
Understanding the Process Behind Professional Packaging Machine Repair
Blog Article
Quick and Reliable Packaging Maker Repair Services to Reduce Downtime
In the affordable landscape of production, the efficiency of product packaging procedures pivots on the dependability of equipment. Quick and trustworthy repair service services are important in minimizing downtime, which can lead to significant monetary losses and functional setbacks.
Importance of Timely Repairs
Prompt repairs of packaging equipments are critical for keeping operational performance and minimizing downtime. In the fast-paced environment of production and product packaging, also small breakdowns can cause significant hold-ups and efficiency losses. Addressing issues without delay ensures that makers operate at their optimum capacity, consequently securing the flow of procedures.
Additionally, regular and prompt upkeep can avoid the acceleration of minor issues right into significant failures, which often sustain higher repair service expenses and longer downtimes. A positive technique to device repair work not just protects the stability of the devices but likewise boosts the general integrity of the assembly line.
In addition, prompt fixings contribute to the longevity of product packaging equipment. Devices that are serviced quickly are less likely to experience too much deterioration, permitting companies to optimize their investments. This is particularly crucial in sectors where high-speed packaging is crucial, as the need for consistent efficiency is vital.
Advantages of Reliable Company
Dependable service providers play an essential duty in making sure the smooth operation of packaging devices. Their experience not only boosts the performance of fixings however also contributes dramatically to the durability of tools.
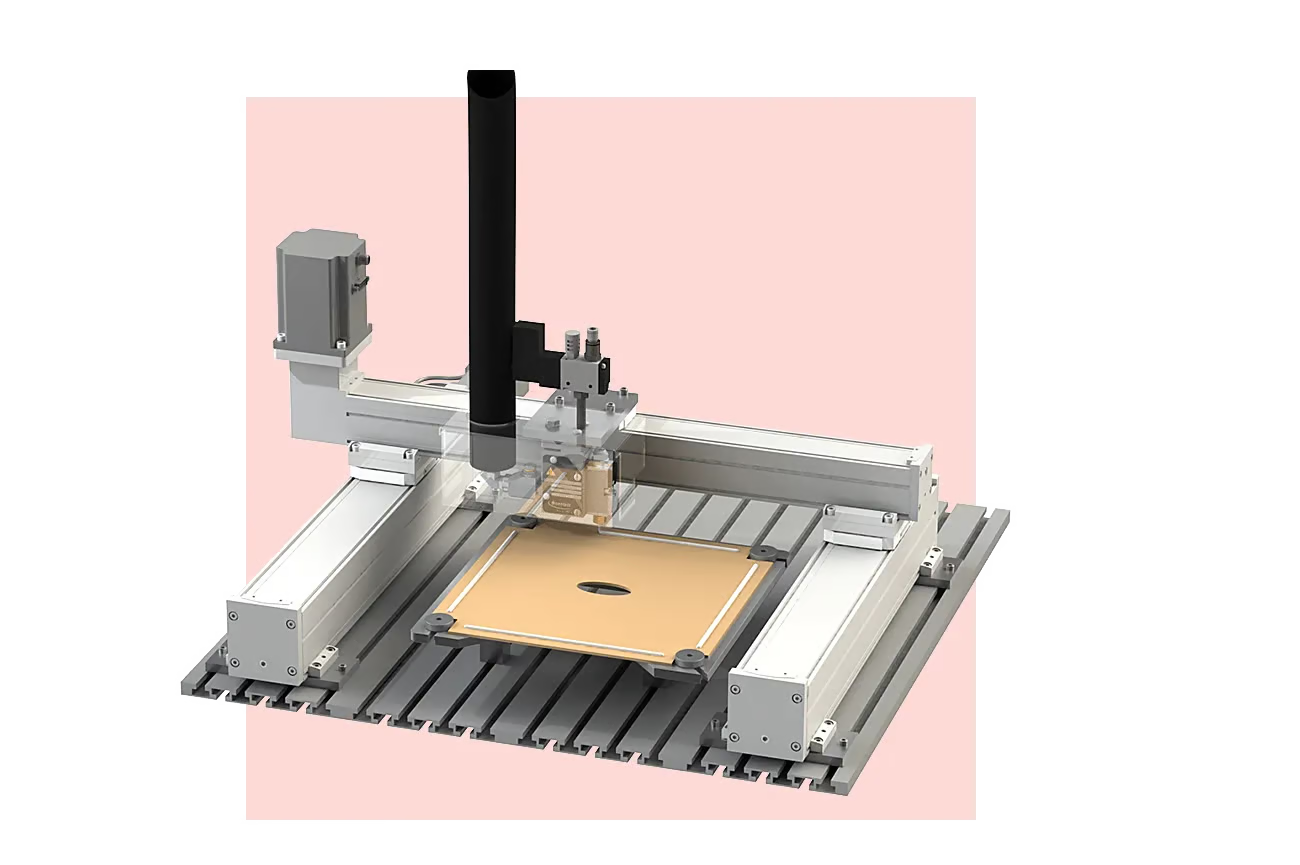
Additionally, a reliable company offers detailed support, including training and support for personnel on equipment procedure and maintenance ideal methods. This not just empowers employees but also cultivates a culture of security and effectiveness within the company. On the whole, the benefits of engaging dependable provider expand beyond immediate repairs, favorably impacting the entire functional process of packaging processes.
Usual Product Packaging Device Problems
In the realm of packaging procedures, numerous issues can jeopardize the performance and capability of equipments. One widespread issue is mechanical failing, frequently originating from wear and tear or inadequate upkeep. Elements such as motors, equipments, and belts might stop working, resulting in failures that stop manufacturing. One more usual issue is misalignment, which can create jams and irregular packaging, impacting product quality and throughput.
Electrical problems can likewise interfere with product packaging operations. Defective circuitry or malfunctioning sensors might lead to irregular equipment actions, causing hold-ups and enhanced functional costs. Furthermore, software problems can impede the maker's programming, causing operational inefficiencies.
Inconsistent item flow is another critical concern. This can occur from variants in product dimension, form, or weight, which might influence the device's ability to manage products accurately. Inadequate training of drivers can intensify these troubles, as inexperienced workers might not acknowledge early indications of malfunction or might abuse the devices.
Addressing these usual product packaging machine issues quickly is important to keeping productivity and making sure a smooth operation. Routine examinations and aggressive upkeep can considerably mitigate these concerns, fostering a trusted packaging setting.
Tips for Reducing Downtime
To reduce downtime in product packaging procedures, executing a proactive upkeep strategy is vital. Frequently set up upkeep checks can recognize possible issues before they rise, guaranteeing equipments operate successfully. Establishing a routine that includes lubrication, calibration, and evaluation of essential parts can substantially lower the frequency of unanticipated malfunctions.
Training staff to operate equipment properly and identify very early indication of malfunction can also play a vital role. Equipping operators with the expertise to carry out standard troubleshooting can prevent minor concerns from triggering significant hold-ups. Preserving an efficient inventory of necessary spare parts can speed up repair services, as waiting for components can lead to extended downtime.
Furthermore, recording maker performance and upkeep activities can assist find out here now identify patterns and reoccurring issues, enabling for targeted interventions. Including innovative tracking modern technologies can offer real-time information, making it possible for predictive upkeep and lessening the danger of unexpected failures.
Finally, promoting open interaction between drivers and upkeep teams makes sure that any irregularities are promptly reported and dealt with. By taking these positive measures, services can enhance operational performance and considerably reduce downtime in product packaging processes.
Selecting the Right Fixing Solution
Picking the appropriate repair work service for packaging makers is an important choice that can substantially impact functional efficiency. An appropriate solution provider guarantees that your equipment is repaired quickly, properly, and to the greatest requirements. Begin by assessing the provider's experience with your details kind of product packaging tools. A professional knowledgeable about your equipment can detect concerns a lot more properly and apply remedies much more swiftly.
Next, consider the solution company's reputation. Looking for feedback from various other services within your industry can give insights right into reliability and high quality. Accreditations and collaborations with acknowledged devices makers can likewise suggest a commitment to quality.
Furthermore, examine their action time and schedule. A solution company who can provide prompt support lessens downtime and keeps manufacturing flow steady. It's additionally essential to ask about service warranty and service warranties, which can show the confidence the provider has in their work.
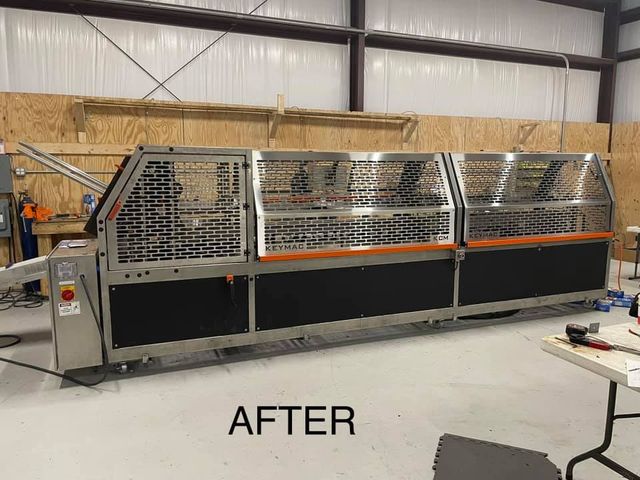
Verdict
To conclude, the relevance of quick and trustworthy product packaging device repair services can not be overemphasized, as they play a critical duty in reducing downtime and guaranteeing functional performance. By prioritizing prompt repair services and selecting reputable solution providers, businesses can properly keep and resolve usual problems productivity. Implementing aggressive maintenance techniques and spending in staff training more improves the longevity of product packaging machinery. Inevitably, a critical strategy to repair services promotes read the full info here a more resilient manufacturing setting.
Prompt fixings of product packaging equipments are essential for keeping functional efficiency and reducing downtime.In addition, prompt repairs contribute to the longevity of packaging equipment. On the whole, the benefits of involving trusted service carriers extend beyond instant repairs, favorably affecting the whole functional operations of product packaging procedures.

Report this page